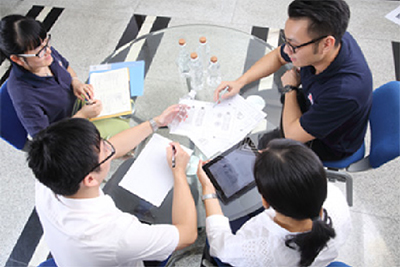
GDXL provides engineering consulting service for PET container projects throughout container design, mold design and manufacturing, container manufacturing, container filling, container treatment and cleaning, conveying, packing, transportation and warehousing. GDXL service team offers flexible and customizable service in three phases of the project:
Pre-project feasibility analysis
Participating in client’s market research and product development, GDXL offers professional technological suggestions on PET package designs, manufacturing equipment selection and investment analysis. It can provide customers with bottle samples for market testing.On-project implementation service
GDXL provides professional advice on customer’s blow molding machine, preform injection equipment and auxiliary accessories to meet specific production requirements. To guarantee the maximum production efficiency, it offers suitable training on operation environment and correct usage on molds.Post-project consulting service
GDXL organizes training courses on technical skills on blowing molding and injection molding, as well as maintenance of mold products.
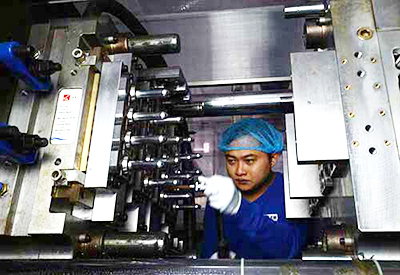
GDXL has over 80 highly experienced and skilled R&D and application engineers to guarantee fast technical support on PET preform complete production line planning, installation and commissioning, mold commissioning, manufacturing parameters adjustment, PET container project consulting, etc. Training courses on PET packaging technology are regularly organized to raise technological level in the industry.
Mold Refurbishment
GDXL provides refurbishment and repair service for blow molds, preform molds and closure molds. Molds are disassembled, inspected and analyzed to diagnose the problem for an appropriate solution. Through mold refurbishment, GDXL helps customers to extend mold service life, reduce mold investment cost and improve the productivity of the mold system.
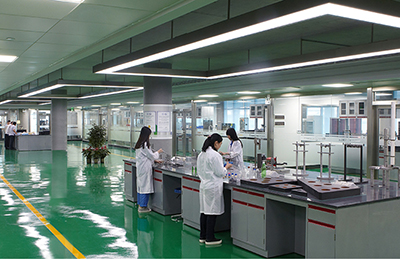
Laboratory
GDXL has a professional laboratory which is among the best in China in terms of inspection capabilities on PET packages and conducts the largest number of corresponding performance tests in the country. It can perform comparison tests and provide reports to customer for realizing inter-laboratory comparison, safeguarding customer’s product quality assurance throughout production. GDXL’s laboratory is the first in the industry to attain national laboratory accreditation issued by the CNAS. It is also certified by Coca-Cola, Pepsi-Cola and Danone as one of their few third party laboratories.
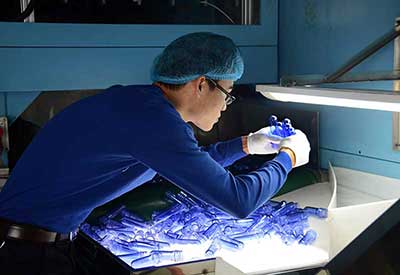
Project Testing Service
GDXL has a team of engineering experts with years of mold manufacturing experience. They are familiar with installation and processing parameters of major brands of bottle blowing, preform injection, closure injection and closure compression equipment, and have accumulated much expertise and experience in mold commissioning. The team is capable of delivering premium and high quality PET engineering service.
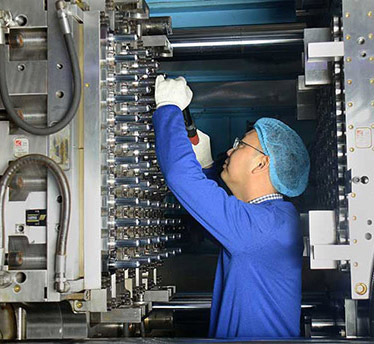
GDXL has a dedicated team made up of 50 R&D engineers and 30 application engineers, which is committed to offering efficient, timely and satisfying after-sales service, including:
- Diagnosis on customer’s production line for improving performance
- Installation and commissioning of preform injection molding system
- Installation and commissioning of mold products
- Emergency technical support and assistance
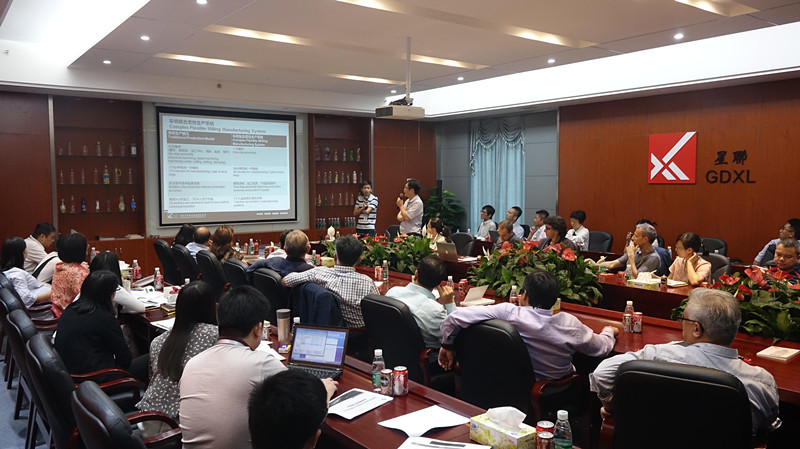
GDXL has 15 professional training engineers to provide customers with detailed training courses on performance optimization, working principles, routine serving and maintenance, and precautions of blow mold, preform mold and closure mold products.
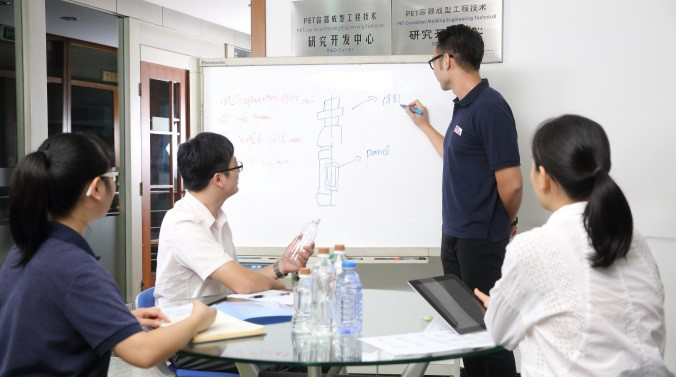
With nearly 30 years of experience in mold manufacturing, a professional team of R&D and after-sales experts, and a world-class laboratory certified by brands like Coca-Cola, GDXL is competent to diagnose and tackle problems on preform, bottle and closure mold products, as well as corresponding molding equipment.
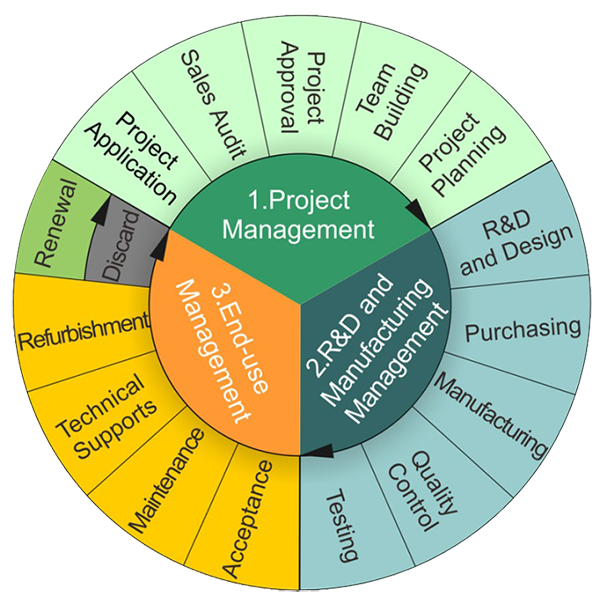
Life cycle management service for mold products is offered to maximize customer’s benefits in the following aspects:
- Timely response to customers’ requirements
- Proposal of precautionary measures
- Solutions to problems occurred during mold product applications, achieving the goals of:
- Maintaining normal operation of mold products
- Building a complete maintenance system for customers
- Raising production efficiency of mold products and extending mold service life